TDK POC
TDK is a japanese multinational that produces electronic materials and components, recording accessories and data storage. Its goal is: "To contribute to culture and industry through creativity"
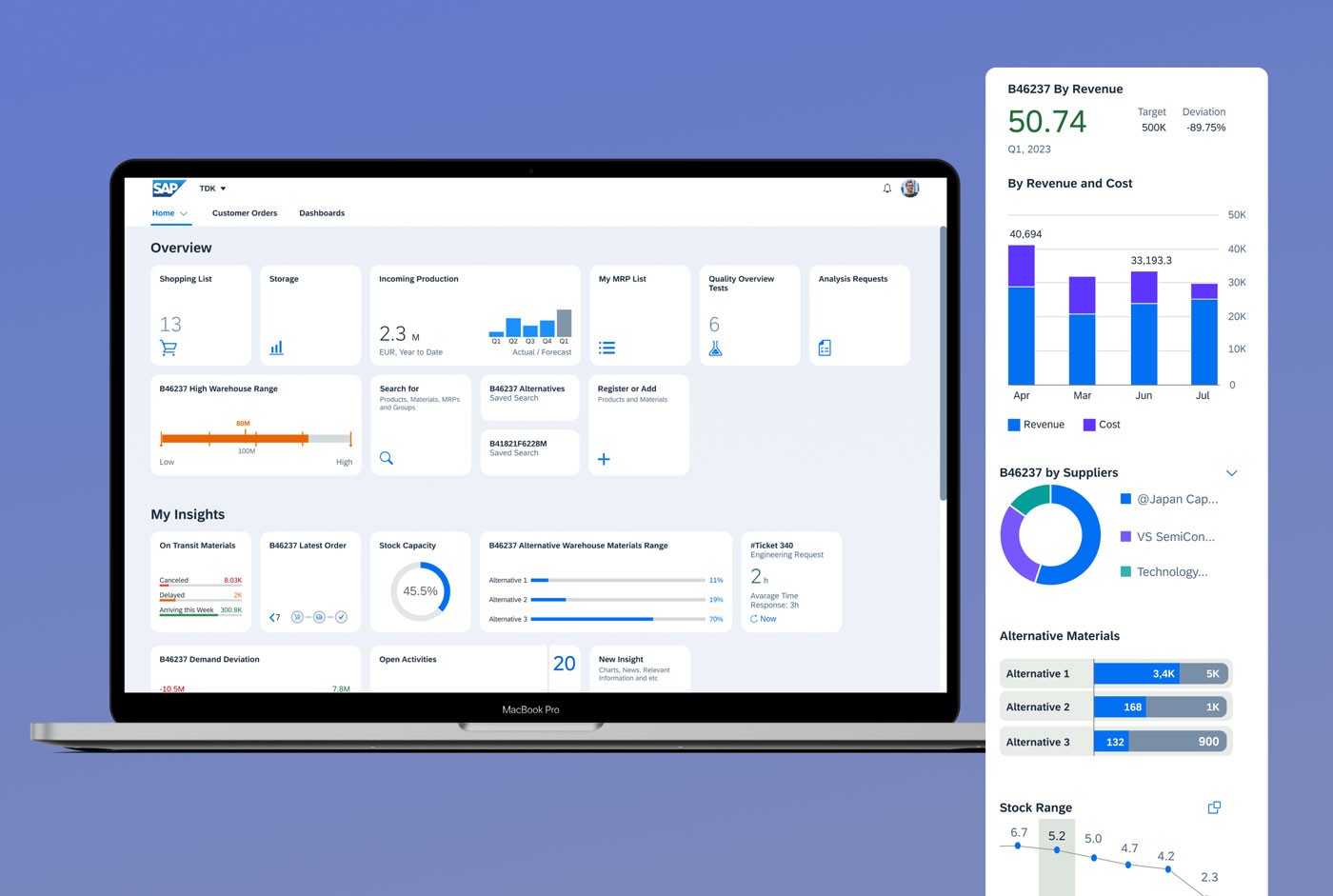
The Challenge
TDK's primary business challenge was managing supply and demand in a volatile market without maintaining large stock quantities. The company aimed for a stock target of 2.5 months and planned demand for the next six months using historical data. However, this approach led to issues such as:
Lack of visibility and knowledge about handling raw materials.
Frequent expiration or neglect of raw materials in stock.
Long logistical processes for new orders of the same materials.
Additionally, when raw materials arrived at the company, they required several experiments by the engineering team before being sent to the factory. The purchasing team also frequently checked with engineering to ensure the materials were useful for production.
Project Team
From TDK: 2 Logistics Analysts, 1 SAP Specialist, 1 Head of Purchasing, 1 Head of Logistics, 1 Head of IT and 1 Engineer
From SAP: UX Design Lead (Me), 1 Design Thinking Facilitator, 1 Product Manager, 2 UI/UX Designers and 3 Developers
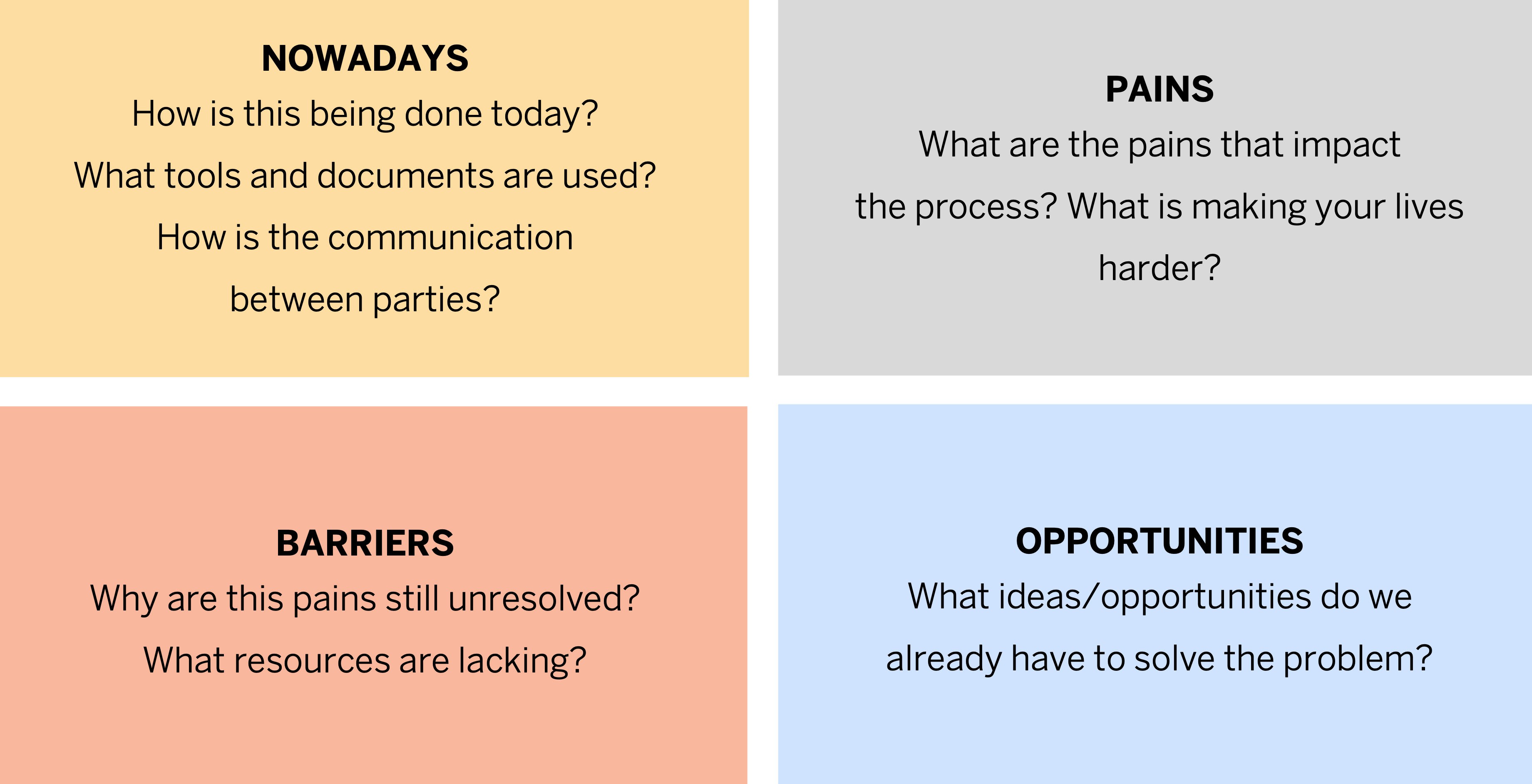
Design Thinking Session - Day 1
The session began with participants divided into three multidisciplinary groups from both companies. The focus areas included:
Identifying the main pain points in TDK’s supply chain.
Clustering findings from brainstorming sessions.
Formulating the critical question: "How can we help logistics analysts make more assertive decisions?"
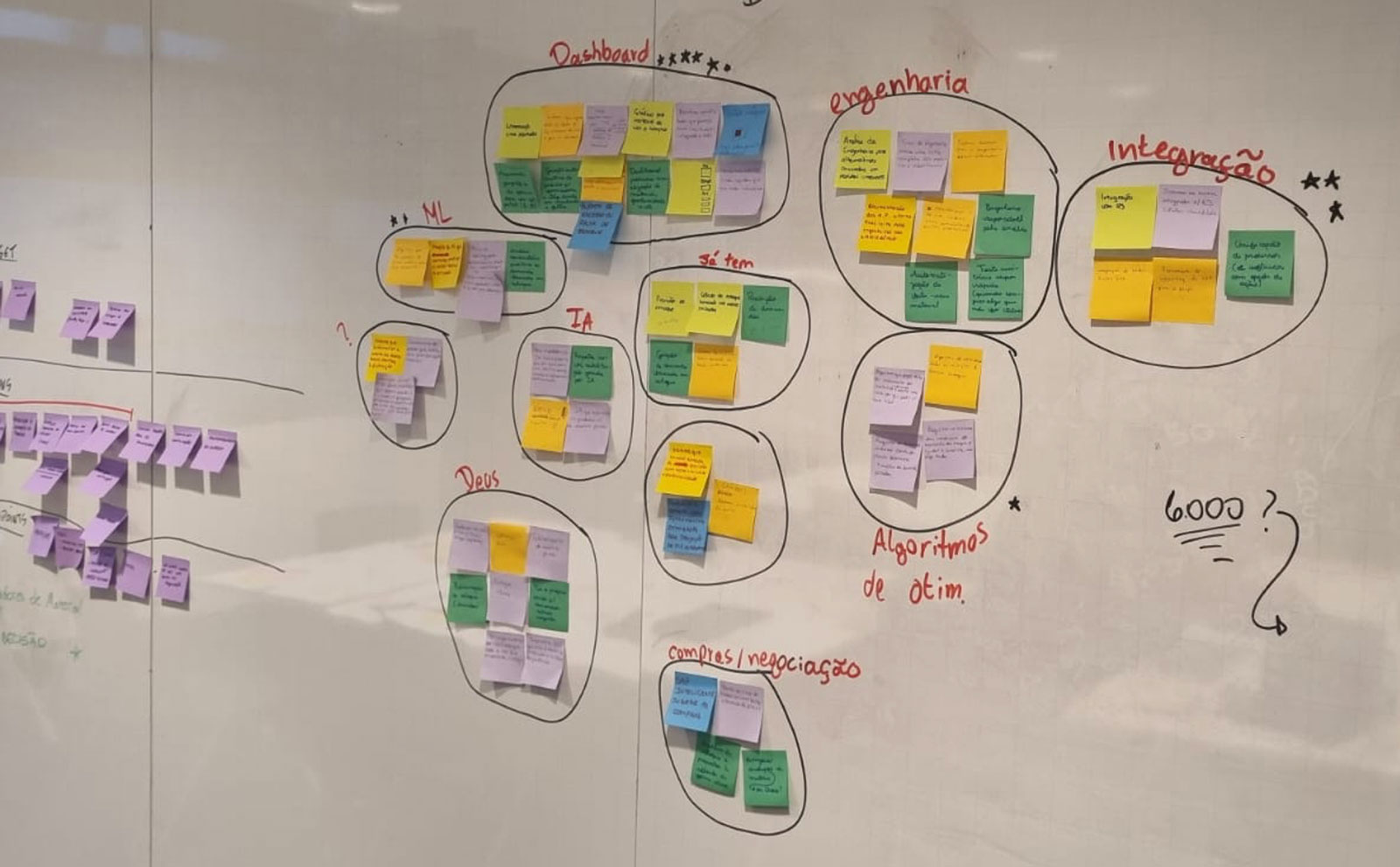
Key Findings
The most significant pain point identified was the vast amount of raw material wasted due to inefficient processes. Raw materials often expired or were forgotten in stock, while new orders for the same materials were being placed, leading to redundancies and inefficiencies.
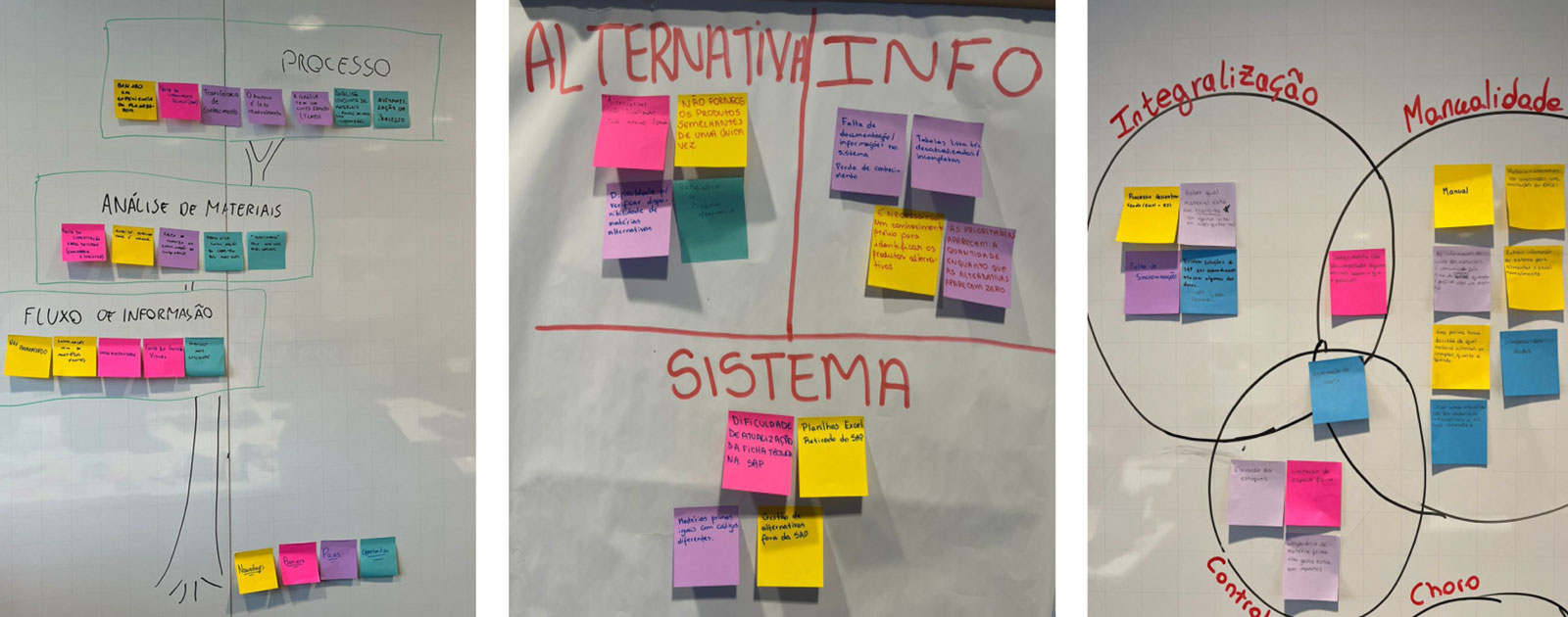
Solution Development
Based on the initial validation of the prototype, the teams proposed an MVP and began developing screens utilizing SAP’s Fiori design system. The development process took a week, expedited by the resources provided by the design system.
Field Study and Validation
A field study was conducted at TDK’s factory to familiarize the SAP team with the physical and digital tools used by TDK. This included:
Observing the factory operations.
Engaging in discussions and alignments with TDK’s team.
Making necessary adjustments based on the observations.
Design Overview
Home
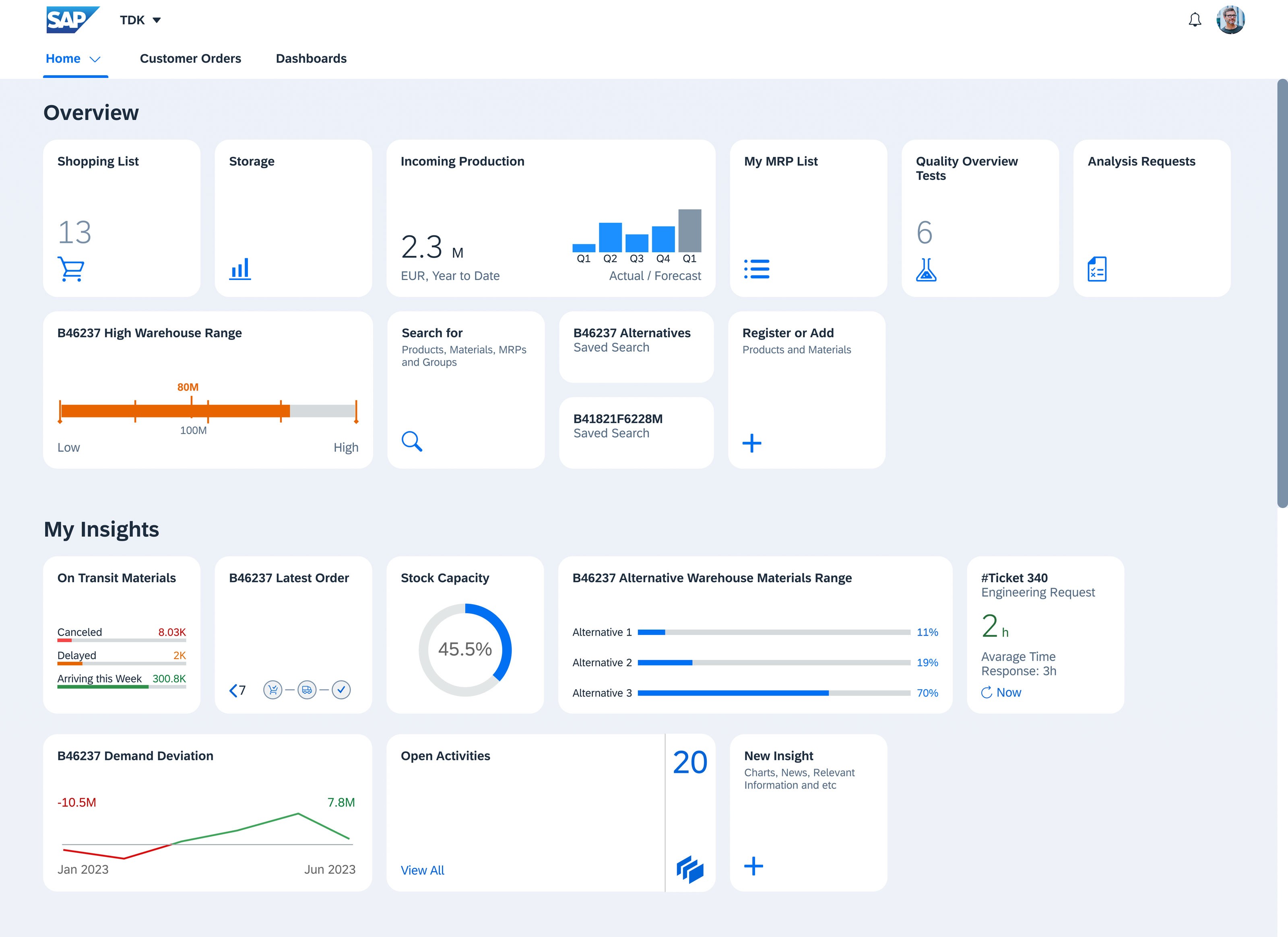
The Home screen provides pertinent information to logistics analysts. It features editable fields for ordering and content management in the lower section, allowing analysts to customize their views and access relevant data quickly.
Stock Material Comparison

This screen includes a table allowing analysts to compare raw materials based on several criteria: validity of materials in stock, quantity in stock, supplier distance, and the quantity reserved for customers. It also offers machine learning-based suggestions for similar chemical products, enhancing decision-making.
Dashboard

The Dashboard screen focuses on groups of materials, enabling analysts to track and manage their assigned products. This helps maintain oversight and ensures efficient handling of materials.
Search by Product
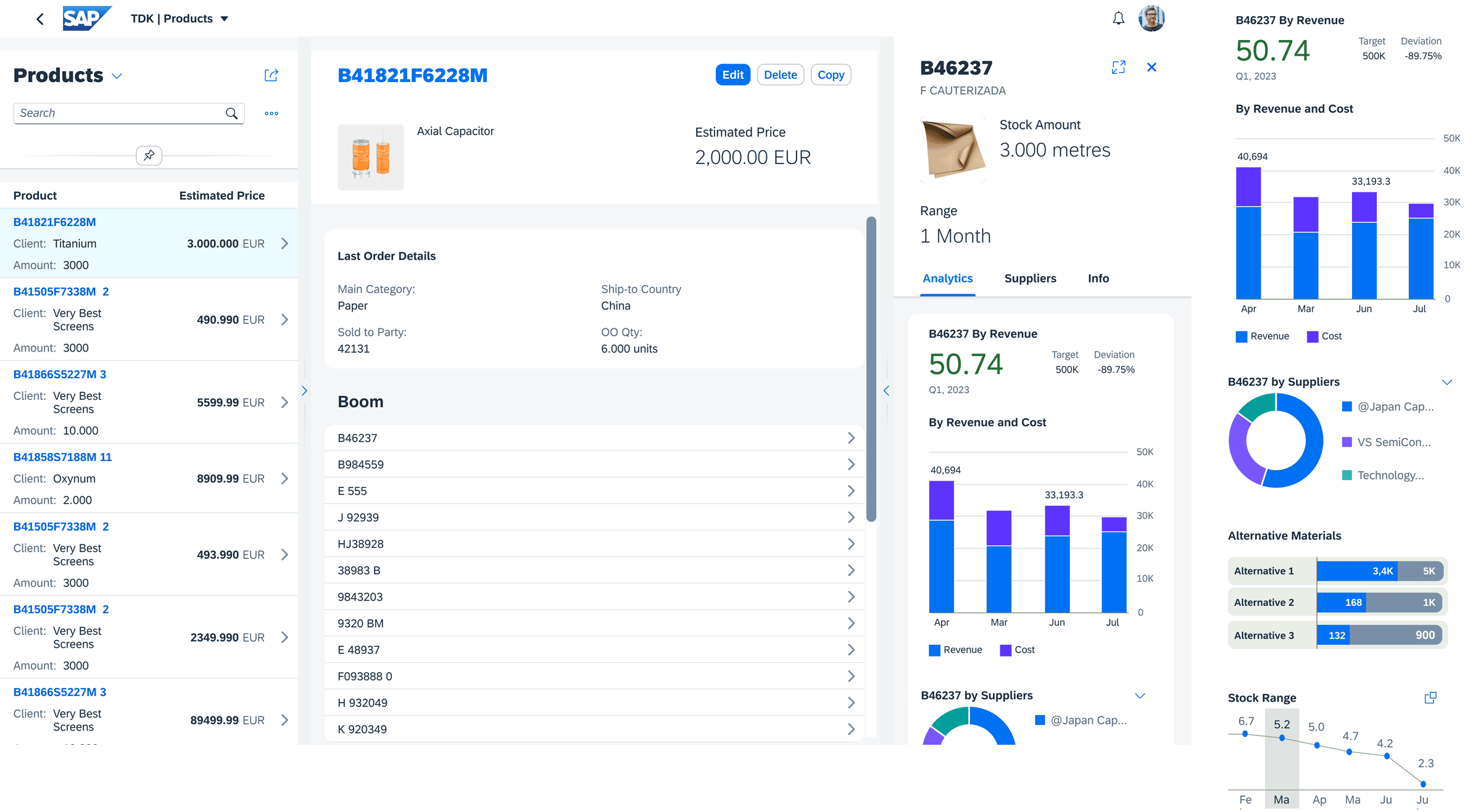
This screen offers virtual stock tracking, allowing analysts to search for products and monitor inventory levels in real-time, enhancing visibility and management.
Conclusion
With TDK’s approval, the Proof of Concept was developed and negotiated with SAP’s sales sector. The project demonstrated the importance of visibility, collaboration, and effective management in optimizing TDK’s supply chain. By leveraging design thinking and SAP’s Fiori design system, the team created a tailored solution that addressed TDK’s unique challenges, paving the way for a more efficient and stable supply chain management process.
Usability Testing